Deployable Force Protection Demo
Survivability demo allows attendees to walk a few steps in Soldiers’ shoes
It is early evening, nearing the end of a long and exhausting day. The relentless sun has yet to show signs of cooling and everyone is hoping for a few hours of relaxation – and then the first explosion sounds. Everyone springs into action as more shots are fired. Dinner is forgotten. The goal now is to stay alive.
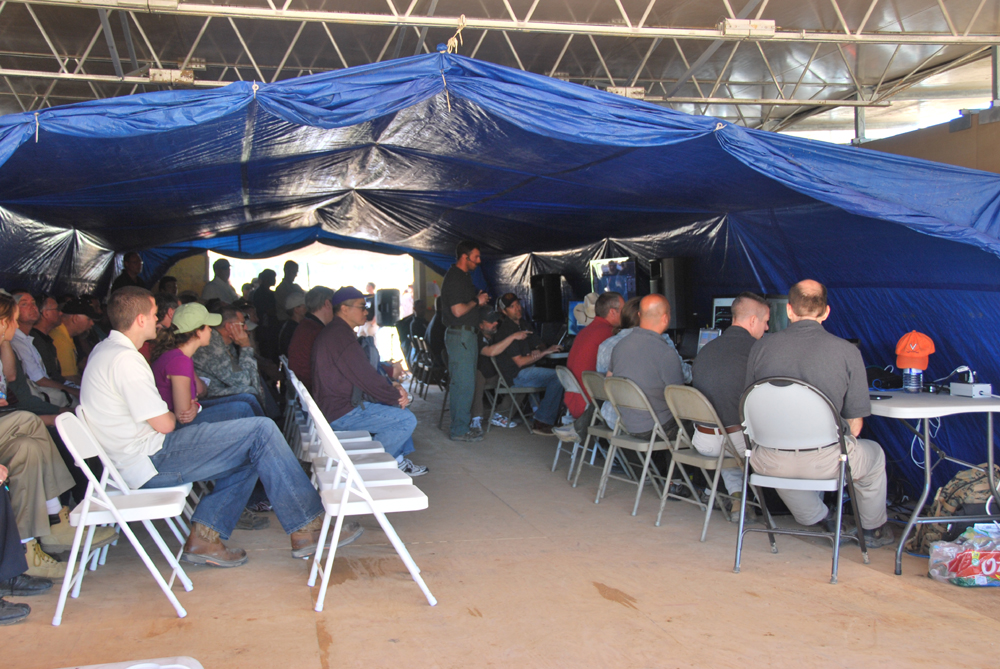 |
Event attendees watch as up and coming computer based software is demonstrated amid simulated fire and sniper attacks during the recent Deployable Force Protection demonstration at Fort Polk, La. Photo by Wayne Stroupe, ERDC PAO. |
A recent Deployable Force Protection (DFP) demo at Fort Polk, La., found attendees in a simulated demonstration of this all too familiar scene. Military and civilian members alike sat quietly as 60 rounds of simulated mortar fire became background noise amid calls of “we’ve detected a sniper along the perimeter wall,” and, “another shot’s been fired.” For those who’d experienced combat firsthand, there were memories. For those who hadn’t, there was a sudden and unavoidable rush of reality.
“In our program, we all feel a personal responsibility to protect our Soldiers,” said DFP Program Manager Jerry Ballard. “I’m not sure we can ever make the battlefield a ‘safe’ place to be, but we should always know that our Soldiers have the best technology working to protect them.”
ERDC’s Survivability Engineering Branch has played an integral role in the DFP Science and Technology (S&T) initiative since its inception – ERDC serves as the lead organization for the initiative, with the Army, Air Force and Navy all heavily involved. The DFP program seeks to develop capabilities that provide additional protection for Soldiers in small forward deployed bases while reducing time and logistic requirements. Success is easily defined as a safe return home for the warfighter.
“These technologies will save lives and reduce injuries,” said Ballard. “We have the ability to improve protection, but we have to be smart in how we do it. If the increased protection requires additional manpower or time to install or maintain, then we’re doing it wrong. The challenge we face is to increase protection without requiring additional Soldier support to use or install it.”
The Fort Polk demo featured a mock combat outpost (COP), put together using a variety of ERDC technologies based around the common building block of the Modular Protective System (MPS), a portable wall made from lightweight space frames and composite armor panels designed to protect against enemy fire. A zigzagged, concertina wire-surrounded path led to an Entry Control Point, the only way to access the inner COP area that included multiple mortar pits, a pedestrian inspection station, a command post and various protective structures.
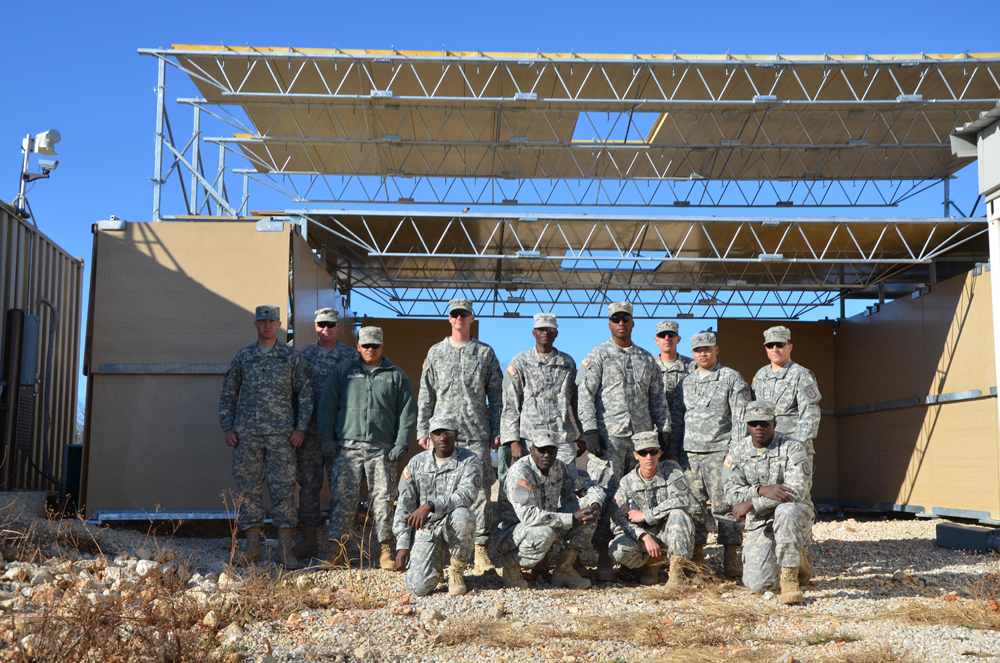 |
Members of the 82nd Airborne Division pose in front of the newly constructed MPS-OHC in Afghanistan. Photo by U.S. Army Corps of Engineers.
|
The first portion of the event concentrated on computer-based software developed by ERDC’s DFP counterparts. Attendees were seated in the COP command post, protected by the MPS Overhead Cover (OHC). Actual Army snipers from Fort Polk, playing the role of enemy snipers, patrolled the perimeter walls and shot with blanks amid simulated and nearby mortar fire, while researchers demonstrated a host of software programs such as Cerberus Skin Detection, Integrated Fixed Site Gunshot Detection System, Non-Line of Sight Cueing and Integration, Leaders Mission Planning Tool, Radio Frequency Direction Finding Sensor, Raw Sensor Data to Information, Target Recognition with Ultra-light Man-Portable Systems, Tactical Imager for Night/Day Extended Range Surveillance, Wide-Area Force Protection, Simple Warning Instant Forecast Tool, Lethal Miniature Aerial Munition System and First Mile Tactical Communications. It was the first time the technologies had been tested together and they meshed well, proving the up-and-coming field has the potential to change warfighter protection.
The following portion of the demo consisted of two blasts designed to test ERDC’s MPS technologies, including the Wall, the OHC, the Mortar Pit, the Multi-Purpose Guard Tower and the Next-Generation Collapsible Truss System. The first blast used mortar rounds strategically placed on the roof of the OHC and near the MPS Mortar Pit. The second blast simulated a suicide bomber in the entry control-point and a vehicle-borne improvised explosive device outside the MPS walls. These explosive events allowed the attendees to witness firsthand the protection capabilities of MPS. Even though the explosions were in close proximity to the MPS, no dangerous fragments passed through the protective systems.
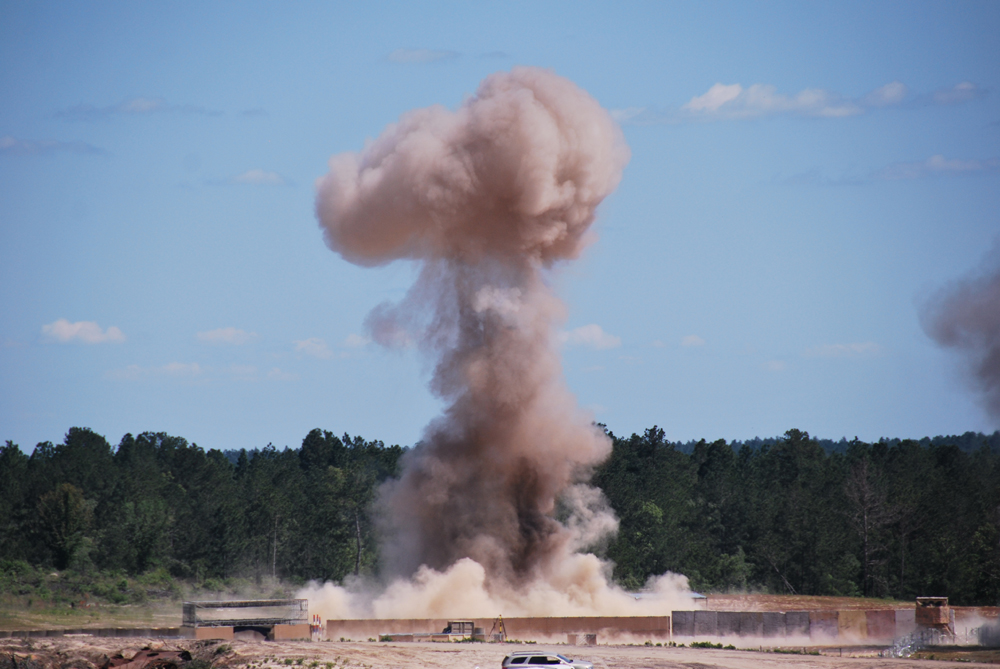 |
A blast simulating a suicide bomber in the entry control-point and a vehicle-borne improvised explosive device outside the MPS walls is seen, part of the recent Deployable Force Protection demonstration at Fort Polk, La. Photo by Wayne Stroupe, ERDC PAO.
|
“This demo included all the active and passive components of the DFP S&T program, so it was much easier to see the whole concept for protecting a COP,” said Nick Boone, a research mechanical engineer with the Survivability Engineering Branch. “Everything went perfectly. The event was well attended and, more importantly, I think everyone learned something. The researchers were given opportunities to challenge their systems and the visitors received a great introduction to the new capabilities.”
While some of the technologies tested are already being used in theater, others are still in the developmental phase. A major benefit of the DFP demonstrations is the ability to test the technology in a life-like environment and use both the results and user feedback to make improvements. The most recent demo was set up to give all technologies, regardless of their readiness level, an opportunity to participate and enhance their system.
“Some found limitations that were easily corrected,” said Boone. “Others received suggestions for improvement that were never imagined. The integration of all the technologies at one site accelerates the development process because you begin to see COP protection as a system rather than a set of individual technologies.”
Such advancements have also allowed multiple versions of the MPS to be placed successfully in theater. The MPS wall was first fielded in Iraq in 2008 and was used by the 555th Engineer Brigade as a temporary perimeter around a short dwell base. Three years later, at a September 2011 demo at Fort Polk, members of the locally-based Joint Readiness Training Center (JRTC) began to take notice of the technology’s ability to be modified to fit a variety of needs. They suggested the MPS-OHC and the MPS Mortar Pit to the soon-to-deploy brigade from the 82nd Airborne Division, calling it a “fit to their mission.”
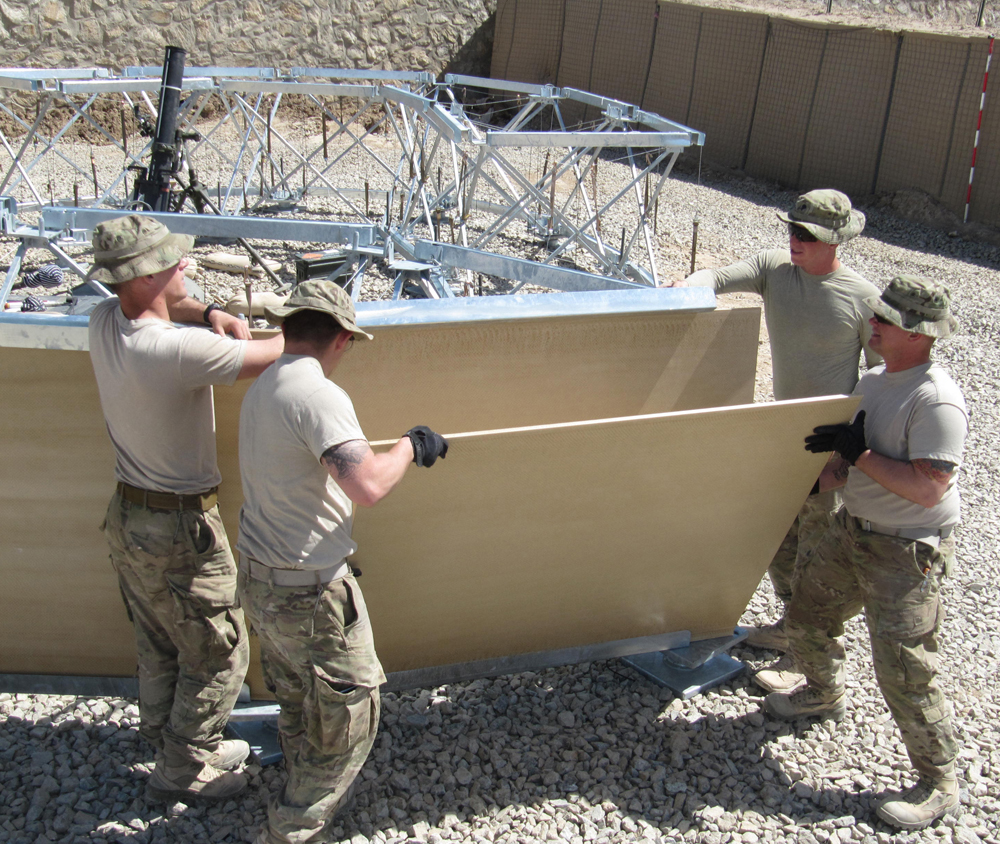 |
Members of the 82nd Airborne Division put the MPS Mortar Pit together in Afghanistan. Photo by CPT Ben Murray. |
It took little convincing for the 82
nd to be on board. ERDC researchers trained the division’s Soldiers on how to use the technology in January, and four MPS Mortar Pits shipped out to Afghanistan with them in April. Also accompanying them was ERDC Capt. Ben Murray, who deployed for two months to help with set-up and gather information based on the technology’s use in theater.
“The mortar position in particular is lacking in force protection,” said Murray. “They liked the system and understood it could be used in many forms. They also liked that it was easy to put up, even for those who had never done it. It’s easy to see the utility in an environment where there’s a lack of engineer support and equipment. The ease of the MPS made a difference for them and, most importantly, it made them feel safer.”
Following the successful deployment of the MPS Mortar Pits, the MPS-OHC arrived in Afghanistan in June. Just weeks after its arrival, the 82nd unfortunately took fire and, though nobody was injured, critical assets were hit. The troops set up the technology to protect those assets the very next day and as word of the protection has spread, MPS variations have continued to be deployed to additional troops.
“This is real-world feedback for us,” said Devin Sham, MPS-Mortar pit developer and survivability research mechanical engineer. “All of the feedback we’re getting continues to be positive. They now have protection in hours, rather than days, and it’s great to see this finally fielded. Knowing we’re making a difference and protecting the warfighter is rewarding. It’s also exciting because we have examples of successful use in theater, something we can use to show that this is more than a theory – it really works.”
“It is extremely satisfying to witness a new product to help Soldiers,” added Boone. “Anything we can do to make their jobs easier is worthwhile. Anything we can do to save their lives is invaluable. And if we can accomplish both, it was a good day.”
Whether you imagined yourself, your loved ones or simply the men and women who are fighting for our country in that original scenario, one truth is inevitable – you want the best protection possible in place, as quickly as possible. ERDC, along with DFP S&T program members, is using events such as the recent demonstration and crucial Soldier feedback to make sure that happens.